Die rund 1350 m lange Rennschlittenbahn in Oberhof erhielt eine neue Überdachung aus frei geformten Schalenelementen aus Holz und Stahl. Aufgrund des Verlaufs und der Geometrie der „Eisschlange“ ist jedes Dachelement ein Unikat.
Im Januar 2023 war Thüringens Wintersporthochburg Oberhof zum vierten Mal Gastgeber der Rennrodel-Weltmeisterschaft. In Vorbereitung darauf sanierte der Zweckverband Thüringer Wintersportzentrum die Rennschlittenbahn, die 1971 errichtet und 2004 erstmals generalsaniert worden war. Neben der grundlegenden Erneuerung der Gebäude, des Haupteingangs sowie des Zielbereichs erhielt die aus Stahlbeton-Segmenten zusammengesetzte Bahnschale im Zug des Umbaus und der Modernisierung eine neue Überdachung. Diese besteht aus frei geformten Holzschalenkonstruktionen.
Ursprünglich war die in Oberhof als „Eisschlange“ bezeichnete Bahn zu 75 Prozent mit Elementen aus Stahl überdacht und erfüllte in großen Bereichen nicht mehr die Anforderungen an den Betrieb einer Rodelbahn. Die Stahlkonstruktion verursachte zudem Kondensatprobleme und damit Tropfwasser, was die Qualität der Bahn stark beeinträchtigte. Durch die neue Holzkonstruktion kann dies künftig minimiert werden.
Anforderungen an die Konstruktion in Holzbauelemente übersetzen
Die Rennschlittenbahn hat eine maximale Wettkampflänge von 1070 m und eine Gesamtlänge von 1354,50 m. Dabei überbrückt sie einen Höhenunterschied von etwa 96 m, hat 14 Kurven sowie eine weitere, nach der Generalsanierung 2004 hinzugefügte Kurve im Auslauf nach dem Ziel.
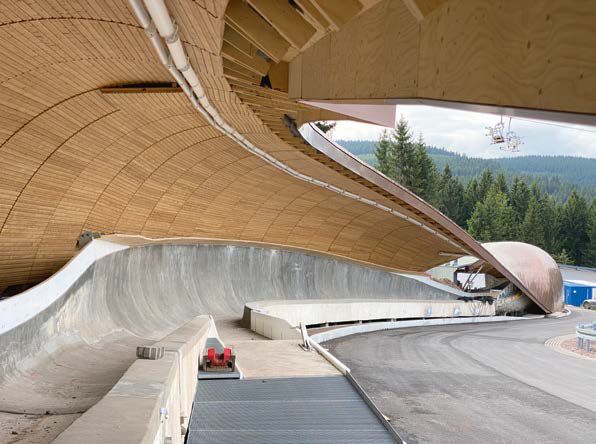
Die beauftragten Büros sprachen sich bereits im Rahmen des VOF-Verfahrens für eine Ausführung der neuen Überdachungen in Holz aus, und zwar mit relativ weitgespannten Bereichen. Bauherr und Nutzer formulierten die wesentlichen Anforderungen an die Überdachung wie folgt: Sie soll vor (Schlag-)Regen, Schnee, Wind und Sonne schützen, die Kondenswasserbildung beim Eisherstellen und in der Nutzung sowie die Kälteabstrahlung minimieren, weitgehende Sichtfreiheit für die Zuschauer und die TV-Übertragung während der Wettkämpfe gewährleisten und zu guter Letzt ansprechend gestaltet sein. Weitere Randbedingungen ergaben sich daraus, dass am Standort der Rodelbahn in einer Höhe von 700 bis 800 m über NN nur eine begrenzte Zeit für die Montage auf der Baustelle zur Verfügung stand und zusätzlich in der Bauzeit auch noch Einzelwettkämpfe, praktisch im Bauzustand, zu ermöglichen waren.
Bereits bei den ersten Entwürfen zeichnete sich ab, dass es sinnvoll war, die dynamische Form der Bahnschale in eine formgleiche Tragwerksstruktur mit Schalenwirkung zu überführen. So, wie die Form der Bahnschale durch die physikalischen Gesetze der Fahrdynamik bestimmt wird, folgt nun die Form der Dachschale den Prinzipien der Statik mit zweckmäßig gewählten Randbedingungen der Stützung. Diese Überlegungen dienten als Basis für die Formfindung der einzelnen Bahnbereiche.
Dabei galt es, vier verschiedene Situationen zu unterscheiden:
a: Die Schale folgt der Kurvenform und setzt direkt auf die Gründung auf.
b: Die Schale setzt direkt auf dem oberen Rand der Bahnschale auf.
c: Die Schale spannt mit geringer Krümmung im Grundriss über eine größere Strecke frei zwischen zwei Kurvenbereichen vom Typ a oder b.
d: Die Schale folgt auf einer langen, geraden Strecke der Bahn und hat nur eine beschränkte Zahl von Zwischenstützungen auf einer Seite.
Diese komplexen Randbedingungen machten schnell deutlich, dass sich die Schalenformen nur mit Freiformflächen beschreiben ließen. Klar war auch, dass die kurze Bauzeit bzw. die sehr kurzen Montagezeiträume einen hohen Vorfertigungsgrad der Elemente erforderlich machten, denn der Zusammenbau konnten nur innerhalb der trainings- und wettkampffreien Zeit zwischen März und September erfolgen.
Aufgrund der statischen Anforderungen und der Montagerandbedingungen entschieden sich die Tragwerksplaner – gegenüber dem ursprünglichen Wunsch nach einer reinen Holzkonstruktion – für eine hybride Konstruktion der Schalenelemente aus Stahl und Holz. Diese bestehen aus gekrümmten Rohrgurten, die mit der Holzschale und ihren Versteifungen schubsteif verbunden sind.
Unterschiedliches Tragverhalten gekrümmter und gerader Streckenüberdachungen
In Bereichen, in denen die Schalen direkt auf der Gründung aufsetzen (Situation a), tragen die Elemente die Lasten vorrangig über Membrankräfte ab, ähnlich wie bei einem gekrümmten Rohrsegment. Entsprechend unterschiedliche Zug- und Druckkräfte ergeben sich in den verschiedenen Auflagerbereichen zur Herstellung des Gleichgewichts.
Ähnlich verhält es sich bei Situation b: Die Dachschalen müssen zusätzlich torsionssteif sein, da sie weniger Schalenfläche mit ausreichender Krümmung aufweisen. Das heißt, die Schalenelemente wirken dann wie ein Ring aus einem geschlossenen Rohr, das am äußeren Rand gestützt wird. Diese Tragwirkung ist umso größer, je größer der überdeckte Winkel des Ringsegments ist.
Bei den Bahnbereichen der Situationen c und d dagegen entfällt die positive Wirkung der Krümmung im Grundriss. Hier kann die Tragfähigkeit nur durch die Krümmung der Schale im Aufriss erzeugt werden. In Situation c können zusätzlich die Effekte aus den Übergängen zu den benachbarten Bereichen mit Krümmung im Grundriss und teilweise auch mit direkt aufstehender Schale genutzt werden. Im Bereich der langen Geraden entfallen solche günstigen Wirkungen jedoch vollständig. Hier galt es, andere wirksame Tragwirkungen zu „wecken“.
Die Haupttragwirkung bei den Übergangselementen besteht im Abtrag der Vertikallasten über die Druckkräfte in die Rohrgurte. Die Holzschale übernimmt die Schubkräfte und gewährleistet in Kombination mit den Schottbögen eine ausreichende Sicherheit gegen lokales und globales Stabilitätsversagen.
Die Aufstandselemente unterscheiden sich von den Übergangselementen dadurch, dass ein größerer Teil der Lasten direkt von den Schottbögen in die Gründung eingeleitet wird. Neben den vertikalen Auflagerkräften wird mit dem Anschluss – je nach Krümmung im Grundriss – auch ein Teil der Einspannmomente aufgenommen.
Im Bereich von längeren Geradenabschnitten sorgen die Einspannungen für die Haupttragwirkungen und sind deshalb etwas kräftiger dimensioniert. Die Aufsatzelemente bestehen aus der oberen gekrümmten Sperrholzschale und der unteren Schale aus einer ebenen Kerto-Q-Platte. Diese beiden Schalen bilden über die Schubkopplungen an den Rohrgurten und an die Schottbögen ein Element mit hohem Torsionswiderstand.
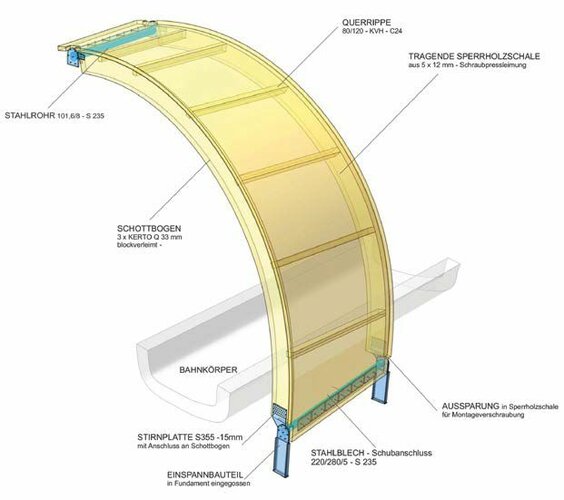
Die Überdachung der Geraden zwischen Kurve 13 und Kurve 14 wird aus vier Einzelsegmenten, bestehend aus zehn Einzelelementen realisiert. Die Einzelelemente sind jeweils zweiteilig mit einer biegesteifen Kopplung der beiden Teile am Druckbogen. Der Anschluss der Elemente an den Druck- und Zugbogen erzeugt eine Einspannung der Elemente in Querrichtung und zusammen mit der Schalenwirkung der Hauptschale wird eine hohe Gesamtsteifigkeit aufgebaut. Die Hauptschale ist hier eine Translationsschale, sodass die Sperrholzschalen nur einachsig gekrümmt sind.
Die vier Einzelsegmente dieses Bahnabschnitts sind zur Minimierung der Höhen und Optimierung der Kamerasicht auf einem Kreisbogen im Aufriss angeordnet, sodass die Hauptebenen zwischen den Einzelelementen hier nicht auf vertikalen Ebenen, sondern auf Ebenen senkrecht zu den Sehnen auf dem Kreisbogen liegen.
Konstruktion und Lastabtragung mit Platten und Bögen
Die Vorfertigung der einzelnen Abschnitte der Bahnüberdachung erfolgte vollständig im Werk. Da die Grundgeometrie der Schalenflächen Freiformflächen sind, hat jedes Einzelelement eine andere Geometrie. Um die geometrischen Anforderungen mit vertretbarem Aufwand beherrschen zu können, legten die Ingenieure als Grundprinzip fest, alle Elementstöße und damit auch die Einzelbauteile im Stoßbereich in vertikaler Ebene anzuordnen.
Dabei bestehen alle Übergangselemente aus den beiden äußeren Rohrgurten (S235 oder S355) mit Schubkopplung an die Schale, den Bogenspanten aus Kerto-Furnierschichtholz, den Querrippen und der aufgebogenen mehrlagigen Sperrholzschale. Die Sperrholzschale ist als Translationsschale mit gerader Erzeugender und zwei gekrümmten Leitkurven im Regelfall doppelt gekrümmt. Die Verwindung dieser Schalenfläche stellt den anspruchsvollsten Teil der Vorfertigung dar.
Die Bogenspanten bzw. Schottbögen sind jeweils aus drei Einzelplatten aus Kerto Q mit 33 mm blockverklebt und komplett mit der CNC-Fräse bearbeitet. Zusammen mit den Querrippen bestimmen diese die Geometrie des Einzelelements. Die vorgefertigten Stahlrohre mit Stirnplatten und Anschlussblechen an die Schottbögen wurden über unterseitig an die Schale angeschraubte Stahlplatten schubfest mit dieser gekoppelt. Die Anpassung an die Winkeldifferenzen erfolgte über Drehung im Bereich des Lochspiels des Anschlusses an das Stahlrohr.
Mit einem Fugenuntermaß von 2 mm ließen sich auch die Fertigungstoleranzen integrieren. Dies hat sich sowohl hinsichtlich des Stahlbaus als auch des Holzbaus als ausreichend erwiesen. Das geringe, aber dennoch vorhandene Quellmaß des Sperrholzes führte dazu, dass sich im Endzustand eine Druckvorspannung zwischen Sperrholzschale und Stahlgurten aufbaute, was sich statisch günstig auswirkt.
Umfangreiche Vorarbeiten fürs richtige Kleben und Fertigen
Wie bei allen Bauwerken mit Freiformflächen waren die Anforderungen an die Planung und Fertigung der Konstruktion ausgesprochen komplex. Angefangen von der minutiösen Vorplanung, damit die Elemente nach der Vorfertigung sowohl in sich als auch im Gesamten zusammenpassten, bis hin zur Fertigung der Schottbögen per Roboter, der Verklebung und dem Abbund der bis zu fünfl agigen und zum Teil doppelt gekrümmten Baufurniersperrholz(BFU)-Schale und schließlich dem Einbau der Stahlteile für die Kopplung der Elemente auf der Baustelle.
So hat man bei Züblin Timber im bayerischen Aichach, wo alle Schalenelemente vorgefertigt wurden, sogar Biege- und Klebeversuche für doppelt gekrümmte Elemente mit Radien unter 2,20 m durchgeführt, um die Machbarkeit solcher Konstruktionen zu überprüfen. Erste Versuche, bei denen die BFU-Platten im Wechsel längs und quer zum Radius verlegt wurden, scheiterten, da die Spannung für die längsverlegten Platten aufgrund des geringen Radius zu groß wurde. Die Lösung für eine funktionierende Konstruktion bestand darin, die Platten ausschließlich quer zur Krümmung zu verlegen. Das hatte jedoch zur Folge, dass keine standardmäßige Schraubpressklebung angewendet werden konnte. In enger Abstimmung mit der Materialprüfanstalt (MPA) Stuttgart und nach bestandenen Tests einigte man sich auf eine Schraubpressklebung mit 12 cm x 12 cm Schraubenraster.
Die Fertigung der Schalenelemente umfasste sieben Arbeitsschritte. Der erste und wichtigste bestand darin, die Kerto-Bögen auszufräsen. Anschließend wurden die fünf Lagen BFU-Platten verklebt. Aufgrund der Verwendung von Resorzinharz konnte pro Tag jedoch nur eine Lage je Element verklebt werden. Bei vier Klebefugen kostete dieser Arbeitsschritt allein vier Arbeitstage pro Element – Züblin Timber hatte damit eine sehr diffizile und zeitintensive Produktion zu bewerkstelligen. Deshalb erfolgte die Fertigung „stufenweise“ auf sechs Montageplätzen. So ließ sich sicherstellen, dass alle Arbeitsschritte kontinuierlich ausgeführt wurden.
Nach dem Fräsen der Kerto-Bögen folgte der Zusammenbau der einzelnen Elemente. Anschließend hat man die Schalen verklebt, abgebunden und die Stahlteile eingebaut. Die Dachschalen erhielten unterseitig – also in den Sichtbereichen – noch eine Bekleidung aus Lärchenholzlamellen mit einer Sichtfuge von 2 cm zwischen den Elementen. Die Lamellen wurden an den Schottbögen bzw. an zusätzlichen Zwischenschotten befestigt und waren Bestandteil der 3D-Modellierung. Sie wurden zum Teil abweichend von der Geometrie der Tragstruktur an den Bahnverlauf angepasst. Als Dacheindeckung dienen 1 mm dicke Schindeln aus eloxiertem Alublech auf Konterlattung und wasserdichtem Unterdach – diese 45 cm x 45 cm großen Schindeln wurden ebenfalls vorgefertigt, aber erst auf der Baustelle angepasst. Alle Elemente erhielten zudem eine Blende am Dachrand, die die Rollos für die Verschattung und den Witterungsschutz aufnehmen und abdecken.
Rundum verpackt wurden die knapp 300 Dachschalen-Elemente mit einer Einzelfläche von bis zu 18 m2 dann zur Baustelle gebracht.
Präzises, zwängungs- und verkantungsfreies Fügen
Die große Zahl an Unikaten des 4500 m2 großen Dachtragwerks war nicht zuletzt auch eine organisatorische und logistische Herausforderung. Denn neben den Entwurfsanforderungen waren in den frühen Planungsphasen nicht nur die Randbedingungen der Vorfertigung zu berücksichtigen, sondern auch die Montagebedingungen vor Ort: Durch die topografischen Gegebenheiten waren die Platzverhältnisse an der Rodelbahn sehr beengt. Die Bahn selbst war für große Transportgeräte nicht befahrbar. So war das Entladen der Elemente nur an einigen wenigen erreichbaren Stellen möglich. Danach mussten sie einzeln per Radbagger zu ihrem Einbauort transportiert werden.
Die Montage erfolgte durch einen regionalen Projektpartner. Dabei wurden die Dachschalen zunächst über einen direkt an der Rodelbahn platzierten Kran an die richtige Position gehoben und so justiert, dass sie exakt montiert werden konnten. Zur Platzierung der Elemente wurde ein spezielles Lastenverteilungsgerät eingesetzt. Der Kranbalancierer ermöglichte es, Kranlasten von bis zu 5 Tonnen mit hoher Präzision und großer Effizienz an den jeweiligen Stellen abzusetzen. Über eine Fernbedienung konnten die Dachelemente exakt in die richtige Neigung gebracht und angeschlossen werden. Das war von elementarer Bedeutung, da ein Fehler bei der Justierung Konsequenzen für alle Folgeelemente gehabt hätte. Die intensive Zusammenarbeit zwischen Planungs-, Ausführungs-, aber auch dem Montagebetrieb samt neuester Maschinentechnik ermöglichte erst das perfekte Ergebnis. Selbst geringe Differenzmaße zwischen Neubau und Bestand im Bereich von 30 mm bis 50 mm konnten geplant und die Übergänge auf der Baustelle problemlos ausgeführt werden.
Bis die gesamte Überdachung montiert und die vorbereiteten Köcherfundamente von den Betonbauern vergossen waren, wurden die Dachschalen-Elemente der verschiedenen Streckenabschnitte teilweise abgestützt oder abgespannt.
Bahn frei für die Rennrodel-WM 2023
Nach Fertigstellung der Überdachung zeigt sich die Anlage weitestgehend stützenfrei. Damit erfüllt sie die modernsten Ansprüche und den Wunsch des Bauherrn nach maximaler Sichtfreiheit. Im September 2022 erfolgten die Übergabe an den Nutzer und die Inbetriebnahme. Die erste offizielle Gelegenheit, die rundum erneuerte Rennschlittenbahn zu testen, bot nun die Weltmeisterschaft im Januar 2023.
Bautafel
Projekt: Umbau und Modernisierung Rennschlittenbahn Oberhof, D-98559 Oberhof
Bauherr: Zweckverband Thüringer Wintersportzentrum (TWZ) Oberhof, D-98559 Oberhof, www.zv-twz.de
Architekten: HSP Hoffmann.Seifert.Partner, architekten ingenieure, D-98527 Suhl, www.hsp-plan.de
Tragwerksplanung und 3D-Modellierung: Trabert + Partner, D-36419 Geisa, www.trabert.de
Werkstattplanung Ingenieurholzbau und Fertigung: Züblin Timber GmbH, D-86551 Aichach, www.zueblin-timber.com
Montage (Holzüberdachung): Züblin Timber GmbH, Strab Ingenieurholzbau Hermsdorf GmbH, D-07629 Hermsdorf, www.strab-holz.de
Montagepartner: Bennert GmbH, D-99102 Klettbach, www.bennert.de